Die Casting in Malaysia: A Pillar of Industrial Growth and Innovation
Die casting is a vital component of the manufacturing industry in Malaysia which is a major contributor to the creation of precision metal parts for various industries. It involves pushing melting metal in a steel mold or die using high pressure. This creates intricately designed pieces with stunning surfaces and precisely-sized measurements. In Malaysia Die casting industry has witnessed constant growth in recent time, driven by the growing demands from major industries like automobile electronic, home, and appliances. Since manufacturers are seeking efficiency and lower cost production techniques and processes, die casting remains an effective solution, especially in mass production, where reliability and speed are essential.
One of the biggest reasons for the need of die-casting within Malaysia is the auto industry. Due to Malaysia being among the major manufacturing centers for automotive that is why the need for light and long-lasting metal parts is essential. Die casting is a method to create parts like engines, gearboxes as well as structural components that are durable and yet lightweight essential in modern automobile design, particularly due to the growing emphasis on the environment and fuel efficiency. Furthermore, as the popularity of electric automobiles (EVs) as well as the development of electric vehicles (EVs), the automobile business requires larger quantities of aluminum parts die-cast for reducing the weight of cars and increase the efficiency of energy. Malaysian die casting firms can meet this increasing demand by providing top-quality components that are compliant with the strictest automobile standards.
Electronics is a major driver in Malaysia’s casting industry. Because Malaysia is one of the major players in electronics production globally Die casting is a crucial process to create the complex metallic components used in electronic devices including laptops, smartphones and household appliances. The high-precision offered by die casting permits manufacturers to design components that have tight tolerances that ensure the durability and efficiency of finished product. Since electronic gadgets are becoming smaller and less sophisticated in their design, the demand for parts that be able to meet the demands of shrinking size has risen. Malaysian die casting firms have been able to adapt by incorporating the latest technologies and methods to create smaller, less complicated parts more efficiently.
Sustainability has become a major issue for the industry of die casting in Malaysia which is in line to global trends towards more sustainable manufacturing methods. This industry is moving to more sustainable methods, including using recycled materials as well as improving the efficiency of energy use during manufacturing. Numerous Malaysian die casting businesses are incorporating sustainable practices that are not just to lessen their carbon footprint, but to satisfy the increasing demands of international customers who prefer sustainable production. Alongside material recycling advances in design of dies like improving the cooling of molds as well as reducing waste, can help companies improve their efficiency and sustainable practices. Sustainability is a key factor in making Malaysia’s die-casting industry as an innovative player in the global market for manufacturing.
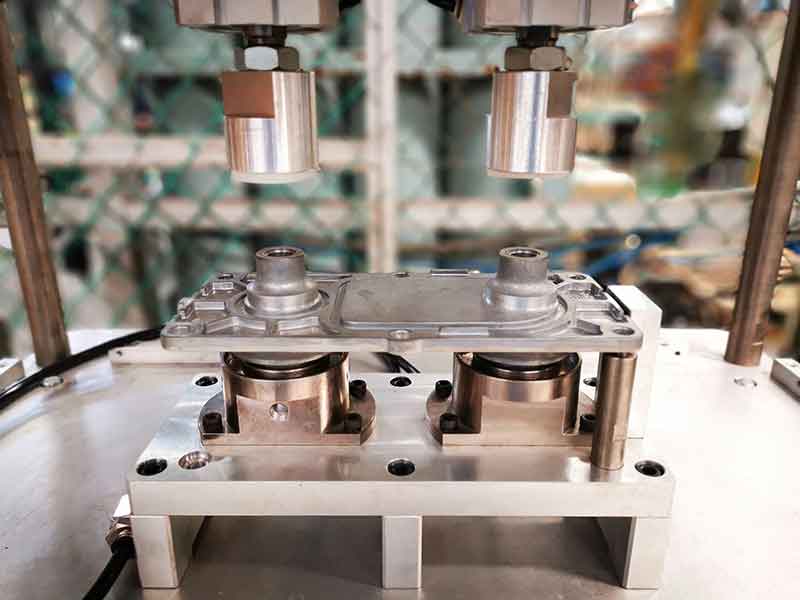
Infrastructure development and the supply of skilled workers are also contributing to the expansion of Malaysia’s die-casting industry. In addition, the Malaysian government has also played the lead in fostering the development of industry, providing incentives, tax breaks as well as facilitating foreign investment in the manufacturing industry. It has encouraged local firms to invest in cutting-edge technologies and die casting equipment to improve the quality and efficacy of their processes. In addition, the focus of Malaysia on vocational and technical training has led to a continuous workforce of highly skilled professionals who have a solid understanding of modern methods of manufacturing. These skilled workers are crucial for maintaining the top requirements for die casting, particularly in the context of greater precision and more intricate production techniques. For more information please Get More Information
Innovation is the mainstay of the industry of die casting in Malaysia and companies are always looking for new ways to increase the efficiency of production and quality of products. Automatization and digitalization in the die casting has enabled companies to create more reliable quality and superior components, while also reducing manufacturing times and human errors. The latest computers-aided design (CAD) and simulation software are being used for optimizing mold designs, which ensures high-quality precision as well as reducing the chance of mistakes in manufacturing. The advancements in technology have allowed Malaysian die casting firms to stay competitive in an ever-changing global marketplace in which speed, quality and efficiency are essential factors in achieving the success of a company.
In the end, die casting in Malaysia is an integral component of the nation’s industry framework. It provides vital components for a variety of industries, such as automotive electronics, electronic and consumer items. Die casting’s capacity to create top-quality metal components that are precision engineered at a reasonable cost is a compelling alternative for production in mass. In addition, with a focus on the environment, sustainable development as well as the creation of highly skilled employees as well, the Malaysian die-casting industry is well positioned to fulfill the increasing demand worldwide for die-cast parts. With industries continuing to develop and focus on efficiency and environmentally responsible practices, die casting is one of the key areas in Malaysia will become a more significant function in the coming years of manufacturing.